Design And Installation Of An LEV System
- RCS
- Dec 7, 2020
- 2 min read
Updated: Apr 7, 2021
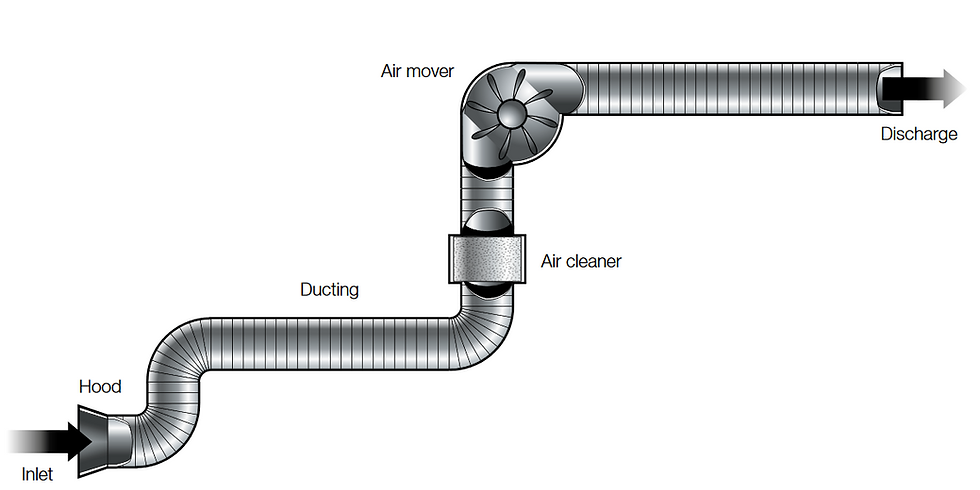
Design is the most important part of any LEV installation and commissioning process. Without correct design, an LEV system will not function efficiently. The specific contaminant will determine the requirements of the Local Exhaust Ventilation system. Once the contaminant has been identified, RCS LEV engineers will design the most appropriate and effective system to remove the contaminant from your work environment.
Design
An LEV system must achieve its specified performance and withstand wear and tear. The components of an LEV system should be easy and safe to check, inspect, clean, maintain and test.
While, designing a system, the following factors must be considered:
A hood or enclosure to collect/contain any contaminants as close to the source as effectively possible;
Removal and transport of the contaminant away from the source via ducting, either venting externally or cleaning and returning air to the building or work area.
An air cleaning device such as a filter, typically located between the hood and fan
An air mover such as a fan to generate airflow

Failure to cover the elements in the diagram above can result in ineffective or unreliable LEV.
Installation and Commissioning
Effective commissioning requires the employer to work closely with the LEV supplier and LEV service providers. Installation and commissioning may interrupt production.
There are four stages to LEV commissioning:
Installation and verifying that the system was installed as designed;
Showing that the LEV system meets the specified technical performance;
Control effectiveness - demonstrating adequate control of contaminant clouds;
Reporting findings as benchmarks for management and maintenance of LEV performance and subsequent examinations and tests.
The LEV commissioning report, together with the user manual, is the basis of the statutory "annual" thorough examination test. Many LEV systems will not have been commissioned or supplied with a user manual. In these cases, the employer will have little information on the required performance or how to maintain it.
LEV System User Manual And Logbook
The manufacturer should supply suitable instructions as part of the design, installation and commissioning process. There should also be instructions on how to operate the system safely, maintain it correctly and examine it thoroughly.
A manual should cover how to use the system, how to maintain it, the spares available and a list of things that can go wrong. It should contain an exploded diagram naming key components of the LEV.
The employer, as owner of the LEV system, requires a user manual because:
They may not understand the technicalities of the LEV system;
LEV checking and maintenance will improve with good instructions and guidance;
It will assist the examination and testing of the LEV system.
An LEV system logbook will contain schedules and forms to keep records of regular checks, maintenance and repair. The logbook will contain:
Schedules for regular checks and maintenance;
Records of regular checks, maintenance, replacements and repairs;
Checks of compliance with the correct way of working with the LEV system;
The name of the person who made the checks.
What Can RCS Do For You
RCS provide Local Exhaust Ventilation solutions for a vast array of industrial air filtration needs. These include hazardous, volatile and explosive dust and fume extraction needs.
We offer a range of services which encompass the entire spectrum of LEV requirements. Services can be purchased individually or as part of a Turn-key solutions package. Call us on +44(0)1563 546807 or click here to contact us for more information.
Comments